Design Factors Affecting the Heat Dissipation Performance of Hydraulic Disc Brakes
by YunaLi on Mar 14, 2025
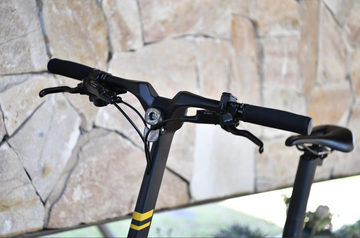
Hydraulic disc brakes are widely used in bicycles, motorcycles, and even high-performance vehicles due to their superior braking power and modulation. However, heat buildup during braking can reduce efficiency, cause brake fade, and even damage components. Understanding the key design factors that influence heat dissipation can help manufacturers and riders optimize braking performance and longevity.
In this article, we will explore the most critical design factors affecting the heat dissipation performance of hydraulic disc brakes.
1. Rotor Material and Thermal Conductivity
The material of the brake rotor plays a significant role in heat dissipation. Common materials include:
· Stainless Steel: Offers good durability and corrosion resistance but has moderate thermal conductivity.
· Aluminum: Lightweight and excellent at dissipating heat, but wears quickly and is less durable.
· Composite & Carbon-Ceramic: Used in high-performance applications, offering exceptional heat resistance but at a higher cost.
Choosing the right material depends on the balance between performance, durability, and weight considerations.
2. Rotor Design and Ventilation
The shape and structure of the rotor significantly influence how well it dissipates heat:
· Vented Rotors: Some high-end disc rotors have internal ventilation channels to improve airflow and cooling.
· Floating Rotors: These allow expansion due to heat and reduce the risk of warping, improving consistency in performance.
· Cutouts and Perforations: Rotors with drilled holes, slots, or wave patterns help increase airflow and reduce heat buildup. However, excessive cutouts may reduce braking surface area and wear faster.
3. Rotor Size and Thickness
Larger and thicker rotors tend to dissipate heat more effectively:
· Larger Diameter: Increases leverage, improving stopping power and spreading heat over a larger surface. Common sizes include 140mm, 160mm, 180mm, and 203mm, with larger sizes preferred for high-speed or downhill applications.
· Thicker Rotors: Retain more heat capacity and resist warping, enhancing long-term reliability.
For high-performance or heavy-duty applications, using a larger and thicker rotor can help manage excessive heat.
4. Brake Pad Material
Brake pads generate friction, and their material impacts heat dissipation:
· Resin (Organic) Pads: Offer quiet performance and good initial bite but may overheat more quickly.
· Sintered (Metallic) Pads: Handle heat better and last longer but can be noisier and wear the rotor faster.
· Semi-Metallic Pads: Provide a balance between heat dissipation and modulation.
Selecting the right brake pad material depends on riding conditions and braking demands.
5. Caliper and Piston Design
The caliper and pistons also play a crucial role in managing heat:
· Multi-Piston Calipers: More pistons (e.g., 4-piston vs. 2-piston) distribute braking force more evenly and help with heat dissipation.
· Material Choice: Aluminum calipers help dissipate heat better than heavier metals.
· Cooling Fins & Radiators: Some high-performance calipers and pads feature cooling fins to enhance heat dissipation.
6. Brake Fluid and Heat Resistance
Hydraulic brakes rely on brake fluid to transmit force. The type of fluid used affects heat performance:
· DOT Fluids (DOT 4, DOT 5.1): Have higher boiling points and better heat resistance but absorb moisture over time, requiring regular replacement.
· Mineral Oil: More stable over time but typically has a lower boiling point than high-end DOT fluids.
For high-performance applications, choosing a brake fluid with a high boiling point prevents brake fade under heavy braking.
7. Heat Sink and External Cooling Enhancements
Some braking systems incorporate additional cooling elements:
· Radiator Fins: Found on certain brake pads and calipers, helping dissipate heat more effectively.
· Heat Sinks: Absorb and spread heat away from critical components.
· Active Cooling Systems: In extreme applications, air or liquid cooling systems are used to enhance heat dissipation.
Final Thoughts
Heat management is a crucial aspect of hydraulic disc brake performance. By optimizing rotor material, size, and design, selecting the right brake pads, and ensuring efficient caliper and fluid performance, riders and manufacturers can significantly improve heat dissipation.
For those seeking optimal braking performance, upgrading to larger rotors, high-performance brake pads, and advanced cooling technologies can make a significant difference, ensuring safer and more efficient braking in all conditions.
Would you like recommendations on specific brake products for your Shopify store? Let us know how we can assist!